Customer: Rexnord, Orange MA
Customers info and needs:
Rexnord manufactures very heavy valves and gates for the liquid flow industry. Most of these parts weigh over 20 tons. The floors in this facility were extremely worn and becoming unsafe to use. Rexnord needed their concrete floor completely resurfaced. They needed a concrete floor topping that would have an extremely high p.s.i. rating as well as be easy to clean, scratch resistant, light reflective and be completely flat. The project would be over 85,000sf and be broken down into 12 phases.
Our specification:
Our estimator specified a 1/4-inch thick, epoxy resurfacer. The resurfacer would be power troweled to get the best p.s.i. rating. All joints would have to be cut and caulked as the floor had much movement. Our estimator also specified a high traffic urethane floor coating as the wear surface. We also recommended yellow, epoxy traffic markings.
Our scope of work:
- Shot blast concrete to prepare for the resurfacing overlayment.
- Saw cut and chase all termination points.
- Apply a 100% solids, epoxy concrete primer.
- Apply the resurfacer at a 1/4-inch using a custom screed applicator.
- Grind entire epoxy resurfacer with concrete grinders.
- Apply a 100% solids, pigmented epoxy grout coat.
- Apply a chemical and wear resistant, urethane floor coating.
The customer was extremely pleased with our work. We were awarded over a dozen more floors at this location after completing this project.
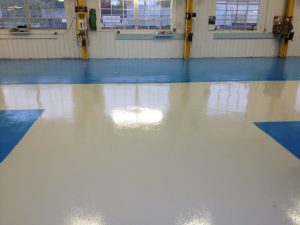
Customer: Kleer Lumber, Westfield MA
Customers info and needs:
Kleer Lumber manufactures a cellular p.v.c. wood product that is super durable, long lasting and looks like natural wood. They needed to expand their growing operation and puchased a 80,000sf building in Westfield MA. This building would be used as their new production facility. The concrete in this building was worn pitted and unsealed. Kleer needed a floor that was easy to clean, could withstand constant forklift traffic, be smooth and seamless and reflect their top of the line product. They are to be coated was approx. 60,000 sf.
Our recommendation:
During our first walk thru, our estimator noticed signs of hydrostatic water vapor. He noticed a white powder along most of the joints and dark areas when he moved a few cardboard boxes that were on site. This meant slab testing was justified. The customer approved testing the concrete. We preformed 30 relative humidity tests. These tests were done in compliance with ASTM standard F2170. The test results were all over 90%. This was 15% higher than a passing score. The customer was not excited about having to add a vapor reducing primer to the floor but was thankful that our company took the time to check a concrete slab that was above grade. The other three bidders missed the potential problem. We recommended a vapor stop epoxy primer, 30 mil epoxy mid coat and a chemical resistant urethane topcoat.
Our scope of work:
- Shot-blast floor as needed when installing a vapor stop primer.
- Fill all major holes, cracks and voids with a cement based mortar.
- Apply the vapor stop primer at a DFT of 16 mils.
- Apply a self leveling epoxy coat at a DFT of 30 mils.
- Apply a chemical and wear resistant urethane at a DFT of 5mils.
This floor came out beautiful and has performed very well.

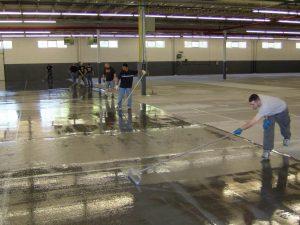
Customer: Judd Wire, Turners Falls MA
Customer info and needs:
Judd Wire decided to update and reconfigure a production line. They abuse their floors with 10,000 lb still wheel carts. They also roll 25,000 led spools of cable over the floor. Judd wanted to update the look of this production area as well as finally putting in a flooring system that would last more than a few months. They also required that the new Flooring be: easy to clean, abrasion resistant, slip resistant, and have clear traffic and production area markings and lines.
Concrete Renovations’ Specification:
After seeing first hand the process in which they more the spools, and seeing the heavy forklift action, we specified one of our most durable flooring systems. We specified a 1/4-inch, epoxy/urethane high wear concrete topping. The aggregates in this floor are comprised of 50% steel and 50% quartz sand.the concrete floor resurfacer is one of the strongest systems we install. The topcoat we specified was a 100% solids, chemical resistant urethane. This urethane is filled with ceramic and aluminum.
Our scope of work:
- Shot-blast concrete floor to remove the failing epoxy floor coatings and to provide the proper surface profile.
- Edge grind entire perimeter where shot-blaster cannot reach.
- Prefill all cracks in the concrete with an epoxy repair mortar.
- Coat the concrete with an epoxy primer.
- Apply the 1/4-inch steel filled mortar with a custom made screed applicator.
- Power trowel the mortar to smooth and compact to attain the highest psi. possible.
- Diamatic surface grind the floor topping to remove any power trowel lines.
- Saw cut all expansion joints, fill with backer rod and a polyurea caulking.
- Apply ampigmented epoxy grout coat at a DFT of 16 mils.
- Seal the flloor with a chemical and slip resistant urethane coating.
This job was installed in early 2015. It has been performing perfectly.
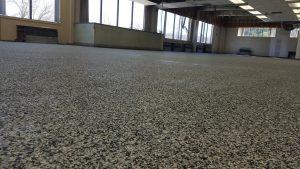
Customer: Fenn Manufacturing, Newington CT
Customer info and needs:
Fenn is mainly a defense contractor. They manufacture fight critical aviation parts. The floor surface they require, needed to be easy to clean, durable, slip resistant and present a world class look. Most of the concrete at this location had been painted with an epoxy paint every year or so. Fenn was tired with the painted look and wanted their customers to be impressed when touring the plant. The total area needing attention was approx. 90,000 sf.
Our recommendation:
We recommended shot-blasting the concrete to remove all the failing floor paint. We specified a 75 mil, epoxy/urethane flooring system. The patching of all the voids would be completed using a fast cure epoxy mortar. Yellow epoxy traffic lines would be installed as needed.
This work would be done in dozens of phases over the course of 3 years.
Our scope of work:
- Shot-blast the concrete to remove the failing paint and to provide the correct surface profile.
- Clean out all cracks and holes using jackhammers.
- Patch all holes and cracks with a fast cure epoxy repair matrix.
- Apply a pigmented epoxy concrete floor primer at a thickness of 10 mils.
- Apply a pigmented, self leveling epoxy slurry at a thickness of 60 mils.
- Apply a pigmented, chemical resistant urethane at a thickness of 5 mils.
- Apply yellow pigmented epoxy traffic markings.
We have been the only contractor to work at this facility for over fifteen years. Needless to say, this customer is very happy.
The installation crews that work in this plant have always been out of our Southwick, MA office.
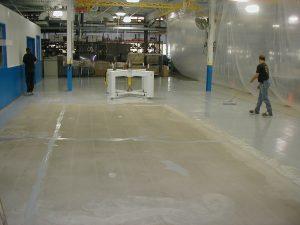
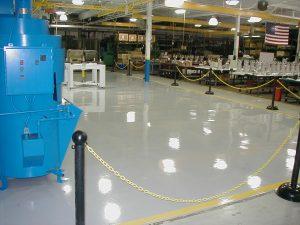
Customer: Ensinger Plastics, Putnam CT
Customer info and needs:
The concrete floor joints were badly deteriorated and the floor was very uneven. The customer wanted a floor that could handle extreme forklift traffic, be easy to clean, light reflective and chemical resistant. They needed the floor to match their first class products. The big challenge would be working around the intense production schedule.
Our recommendation:
We specified a 1/4 inch, power troweled epoxy resurfacer with an epoxy mid coat sealed off with a high traffic urethane top coat. This Tennant Company concrete resurfacer would have to be installed on weekends, at night and in 12 phases.
Our scope of work:
- Attend a preconstruction meeting
- Shot-blast floor to achieve the proper surface profile
- Saw cut and key in all termination points
- Fill all the holes, cracks and voids with an epoxy mortar
- Power trowel out a 1/4 -inch epoxy resurfacer
- Grind floor to remover any trowel marks
- Apply a 100% solids epoxy grout coat
- Apply a 100% solids high wear urethane seal coat
- Cut and fill all expansion joints with a polyurea
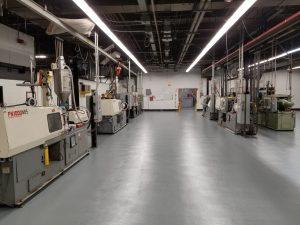
Customer: Covestro South Deerfield, MA
Customers info and needs:
Covestro is a leading producer of advanced polymers and high-performance plastics in North America and around the world. The concrete floors in this project were not previously coats with anything. They were bare and had worn badly in some areas. Covestro wanted to update these areas with a flooring system that would be light reflective, chemical and wear resistant, seamless and extremely durable. They also wanted 2 Covestro logos in the floor. This area would be approx. 10,000sf.
Our recommendation:
We specified a Tennant Company, 60-mil, self leveling epoxy with a high performance urethane. The joints in this area were deteriorated and needed to be repaired. We specified diamond grinding to prepare the concrete floor for the new system.we also recommended installing yellow traffic markings.
Our scope of work:
- Diamond grind entire concrete floor to provide the proper surface profile.
- Prep and repair floor joints with an epoxy repair matrix.
- Grind repairs smooth.
- Prime floor with a pigmented epoxy floor primer.
- Apply the 60-mil, self leveling epoxy to the floor. Cut and caulk control joints.
- Apply the high performance urethane topcoat
- Install 4-inch epoxy traffic markings.
- Install 2 Covestro Logos.
This project came out perfect. The customer was very pleased. We have completed many addition floors for this customer.
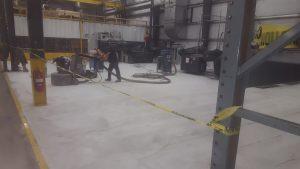
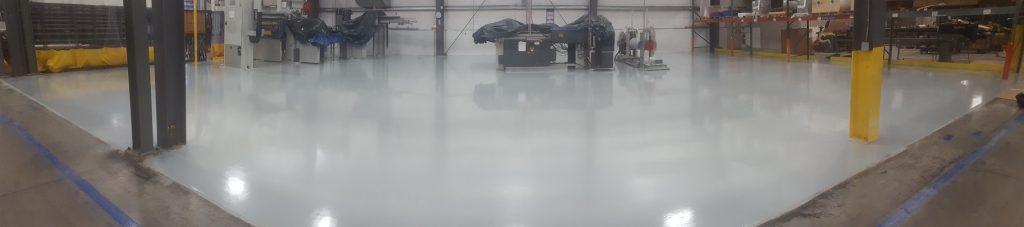
Customer: Sheffield Plastics, Sheffield MA
Customer info and needs: Sheffield Plastics is a producer of all types of polycarbonate goods. The concrete in most of the buildings in this location is unsealed. Sheffield wanted to update a few of the floors in 3 production areas. They needed the new surface to be smooth, easy to clean, chemical resistant and extremely durable. The square footage for this project was 23,000 sf.
Our recommendation: We specified a Tenant Company, 85 mil, epoxy/ urethane flooring system.
The method of preparation for this project would be shot-blasting. All damaged concrete would be prepared and patched with an epoxy repair matrix. The work would need to happen Fridays thru Sundays.
Our scope of work:
- Shot-blast concrete to attain the correct surface profile.
- Prepare and patch all cracks and holes with an epoxy repair mortar.
- Apply Tenant Eco-Fsc epoxy primer, at thickness of 12 mils
- Apply Tennant Eco-Mpe slurry coat, at a thickness of 60 mils.
- Sand and auto scrub entire floor.
- Apply Tennant Eco-Hts urethane, at a thickness of 5 mils.
- Apply yellow epoxy traffic lines.
The floors came beautiful. The customer was very happy. Due to the success of this first project, we have installed many floors for this customer over the last 15 years.
The floors we have completed at this facility have been installed by our Albany, NY and Southwick, MA crews.
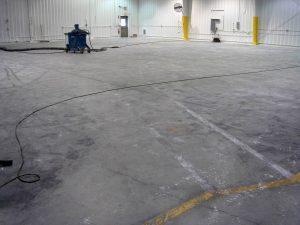
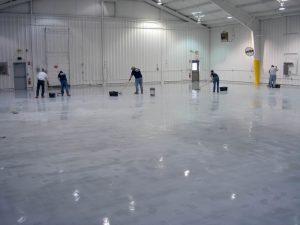
Customer: Arwood Machine Company, Newburyport MA
Customer info and needs: Arwood Machine is a precision contract machining facility. Their primary customers are from the medical and defense fields. The production floor at this location is over 100,000 sf. The president wanted to brighten up the look of the shop by having new traffic lane flooring installed. Arwood needed a floor surface that was light reflective, durable, wear resistant and easy to clean.
Our recommendation During our walk thru, our estimator noticed signs of water vapor. He had one of our technicians perform a relative humidity test. This test failed. Due the failure we specified a vapor stop primer. For the flooring system we specified a 50 mil, epoxy/ urethane coating. The owner chose white with blue safety lines.
Our scope of work:
- Shotblast concrete to provide the proper surface profile.
- Fill all holes and voids with a vapor stop slurry.
- Apply the vapor stop epoxy at a thickness of 16 mils.
- Broadcast aggregate to excess.
- Apply an epoxy base coat a t a thickness of 15 mils.
- Apply a self leveling epoxy slurry at a thickness of 30 mils.
- Apply a chemical and UV resistant urethane at a thickness of 5 mils.
- Apply blue epoxy traffic markings.
The customer was very happy with the new floor. We checked in in this location 8 years after the floor had been installed and it still looked great.
The crew responsible for this install was from our Southwick, MA location.