Customer: Plimpton & Hills, Stamford CT
Customers info and needs:
P&H wanted to renovate their 10,000sf showroom in Stamford CT. The existing floor was about 15 different types of tile and hardwood. We had polished the concrete at a few of their other locations. It served them well. This floor would have to be broken into two phases. They needed to keep half of the showroom open. P&H has its own maintenance people so they would remove the existing flooring materials.
Our recommendation:
We recommended that the customer allow us to remove the grout materials that were left behind after removing the tile. We could remove it whiteout damaging the concrete. We would then fill all holes, cracks and voids with an epoxy repair matrix. Finally polishing the concrete to an 800 finish topped by a stain inhibitor.
Our scope of work:
- Remove existing grout from the concrete using diamond grinders.
- Cut and caulk all joints with a flexible, polyurea joint material.
- Grind concrete floor with 30/40 and 60/80 grit diamonds.
- Grind entire concrete floor with 50 and 100 grit, ceramic bond diamonds.
- Polish entire concrete floor using 200,400 and 800 grit, poly bond diamonds.
- Apply a stain inhibitor and burnish.
The customer was very happy with this floor. This was the 5th location. We have polished in CT for this customer.
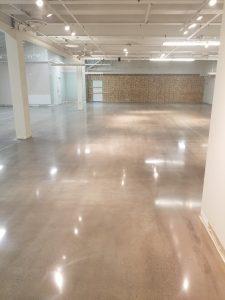
Customer: Formula Powerboats Northeast, Norwalk CT
Customer info and needs:
Formula Powerboats Northeast is one on New England’s largest powerboat dealers. This location has a full retail store, maintenance shop, marina and indoor showroom. Formula wanted to freshen up the look of their 16,000 sf showroom. The floor was covered in carpet squares that did not hold up well The constant moving of the boats destroyed the carpet. The customer removed their own carpet tiles and hired us to provide them with a floor that was easy to clean, dust proof, stain resistant decorative and that would hold up to the trailer tires.
Our recommendation:
We recommended that the concrete be polished to a level 4 finish. We also recommended that the holes and joint be filled and repaired.
Our scope of work:
- Grind entire concrete floor with 40 grit diamonds on dust controlled grinders.
- Prep and patch all holes and joints.
- Grind entire concrete floor with 80 and 100 grit diamonds on dust controlled grinders.
- Apply a concrete densifier.
- Polish concrete with 200,400 and 800 grit diamonds on dust controlled polishers.
- Apply a stain blocker.
- Burnish entire floor .
The concrete polished very nicely. The customer was thrilled.
This work was performed by an installation crew from our Middletown, CT offices.
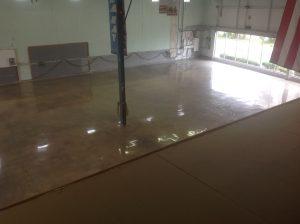
Customer: Cabot House Furniture, Framingham MA
Customer info and needs:
Cabot House purchased an building that previously used as a banquet hall and restaurant. They wanted to use the location as a high end furniture showroom. Cabot House wanted the existing concrete floor polished. One of he biggest challenges with this concrete slab was that it had thousands of holes where walls had been in the past. It also had hundreds of holes that had been filled with a leveler. This light color in the holes would have to be removed.
Concrete Renovations’ Solution:
We specified that concrete should be grinder with 30/40 grit metal diamond to remove the mastics and sealers. Then all the holes and joints filled with the light colored repair mortar be removed. All the holes would then be filled with an epoxy matrix. The floor would then be polished to an 800 finish and stain guarded.
Our scope of work:
- Grind floor to remove all mastics, sealers and patches.
- Remove all light colored patch materials with saws and jackhammers.
- Patch all holes and voids with an epoxy repair material.
- Grind entire concrete floor with 30/40 and 60/80 grit metal diamonds.
- Grind floor with 100 grit ceramic diamonds.
- Apply a concrete hardening liquid.
- Polish concrete using 200, 400 and 800 grit poly diamonds.
- Wash concrete with a ride on Tennant Scrubber.
- Apply a concrete sealing stain guard.
This floor exceeded the customers expectations. We have since polished a second location for them.

Customer: ADP Proxy, Comack NY
Customer info and needs: ADP in Comack, NY is a proxy mailing facility Most of the worlds fortune 500 Companies use this service. ADP added an additional 400,000sf to their existing building. They wanted a coating on the new concrete floor that would be easy to clean, light reflective, durable and dust proof. ADP also needed all the control joints filled. The area to be coated in one phase was 390,000 sf. The joints to be filled were approx. 3.5 miles. The installation window was only 14 days.
Our recommendation: We recommended a shot-blast preparation method and a 32 mil, epoxy flooring system. We specified the joints be cut and filled with a polyurea joint filler.
Our scope of work:
- Shot-blast floor to provide the proper surface profile.
- Saw cut and fill all control joints.
- Apply a high solids epoxy primer at a thickness of 12 mils.
- Apply a 100% solids epoxy mid coat at a thickness of 22 mils.
- Apply a 100%solids, orange peel, epoxy topcoat at a thickness of 8 mils.
Job notes: This job was high profile and fast track.
Our aggressive schedule was as follows:
- Days 1 and 2- Cut and fill all joints. This was done in two days by running 4 crews around the clock.
- Days 2 and 4- Shot-blast entire floor. This was done by running 4 machines around the clock .
- Day 5- Vac and wash entire floor. This was done by running 3 Tenant, ride on scrubbers.
- Days 6 and 7- Primed the entire concrete surface. This was done by having 22 installers and 4 mixers.
- Days 8 and 9- Mid coated entire primed floor. This was done by having 26 installers and 6 mixers.
- Days 10 and 11- Top coated entire floor. This was done by having 26 installers and 4 mixers.
The customer was extremely happy and impressed that we completed the floor 3 days early.
Since this project we have completed 3 other floors for this customer.
To complete this floor so quickly, we pulled installation teams from our Boston MA, Albany NY, Middletown CT and Southwick MA locations.
Customer: Best Buy, Milbury MA
Customer info and needs: Best Buy needed to upgrade the look of their car audio installation bays. The existing concrete was had holes, cracks and was dusty and unsealed. Their technicians needed a floor that was dust free, easy to clean and was wear and slip resistant The installation bay was 1,640 sf.
Our recommendation: Best Buy has a certain floor coating in all their locations. The system is a Tenant Company, ECO-MPE/ ECO-HTS Coating. This is a high quality 30 mil floor coating. Best Buy Specifies a black floor with yellow stripes.
Our scope of work:
- Diamond grind concrete to create the proper surface profile.
- Patch all holes with an epoxy patch matrix., grind smooth after cured.
- Apply ECO-MPE Epoxy Primer at a thickness of 10 mils.
- Apply ECO-MPE Epoxy Mid Coat at a thickness of 16 mils.
- Apply ECO-HTS Urethane at a thickness of 4 mils.
- Apply ECO-MPE Epoxy traffic lines.
Best Buy was very happy with the floor coatings. This was our first car audio bay. We have completed epoxy coatings in 5 other locations since.
The crew used on this install was from our Cambridge Ma Office.
Customer: Hoffman Audi, East Hartford CT
Customer info and needs: The Hoffman Auto Group decided to open an Audi Dealership in East Hartford Ct. The building would have a 12,000 sf service department. Hoffman wanted an epoxy flooring system in this area because they needed a floor surface that would be easy to clean, slip and impact resistant, durable and have a world class appearance.
Our recommendation: We specified a 1/8th inch, epoxy/urethane, shop floor system. We specified shot-blasting as the method of preparation and safety stripes around the work areas.
Our scope of work:
- Shot-blast concrete to attain the proper surface profile.
- Apply a 100% solids, pigmented epoxy primer.
- Apply a 100% solids, pigmented epoxy base coat.
- Broadcast aggregate to excess.
- Apply a 100% solids, pigmented epoxy base coat.
- Broadcast aggregate to excess.
- Apply a 100% solids, pigmented epoxy grout coat.
- Apply a 100% solids, chemical resistant urethane.
- Apply epoxy traffic stripes.
This project came out flawless. The customer was very happy.
The installation team that installed this project was from our Southwick Ma office.
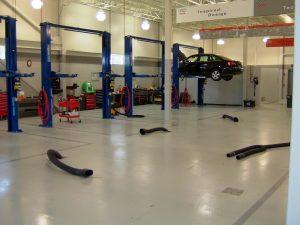
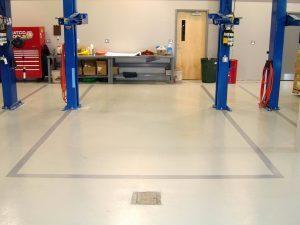